Från rågummi till
bildäck m.m. Norstedts filmband.
|
|
|
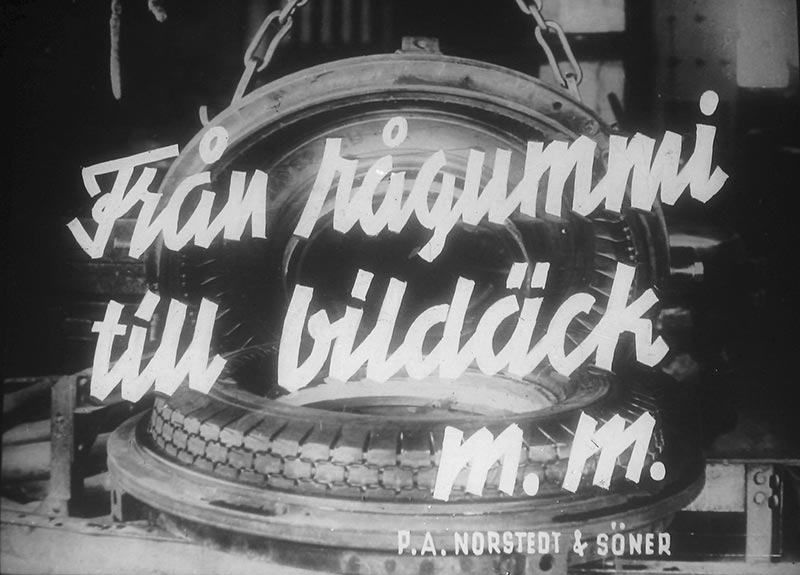 |
Först under förra hälften av 1500-talet blev kautschuken känd av europeerna.
Det var då spanjorerna på sina vidsträckta resor kommo till Amerika och
funno att indianerna bedrevo ett spel med egendomligt studsande bollar, som
voro gjorda av ett slags harts, vilket de fingo av ett träd, benämnt
Ulé-trädet.
Närmare kännedom om detta ämne fick man dock ej förrän under 1700-talet.
Då utsändes från Frankrike ett flertal vetenskapliga expeditioner till
världens olika länder och en af dessa kom till Syd-Amerika. Där påträffades
åter detta slags harts och det beskrives i en vetenskaplig avhandling på
följande sätt: "Det växer i urskogarna ett träd, från vars bark om denna
såras, flyter fram en vit vätska, liknande mjölk. Denna vätska hårdnar så
småningom och mörknar. Infödingarna gör facklor därav, som brinna bra utan
vekar och ge ett klart ljus. De bekläda även tygstycken därmed, vilka sedan
användas för samma ändamål, som vi ha vaxduk. Ävenså tillverka de skor av
detta material. Dessa skor äro vattentäta och om de hållas i rök svärtas de
och få utseende av vanligt läder". Indianerna hade således redan långt
tillbaka i tiden kännedom om kautschukens egenskaper.
Den första gummifabriken anlades år 1820 i England. Sedan emellertid den
första nyfikenheten gått över blevo gummivarorna impopulära på grund av de
stora olägenheter, som ännu vidlådde desamma. Produkterna voro alltför
mycket beroende av temperaturen. Vid vanlig rumstemperatur voro de elastiska
men blevo vid hög temperatur klibbiga samt vid kyla hårda och spröda. Dessa
olägenheter lyckades en amerikansk gummifabrikant, Goodyear, borteliminera
genom att uppvärma rågummi tillsammans med svavel. Senare fann man att ännu
bättre resultat uppnåddes om råvaran behandlades i ett svavelbad. Gummits
behandling med svavel har fått namnet vulkanisering.
|
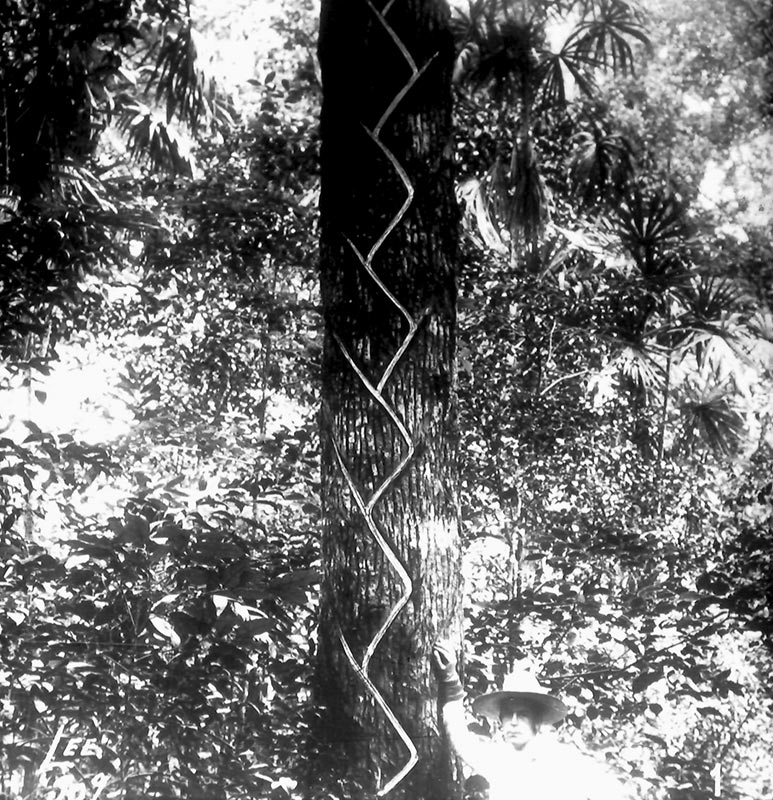 |
1. Den förnämsta kautschukförande växten är Hevea brasiliensis. Det är ett
stort träd, härstammande från urskogarna omkring Amazonfloden, där det når
en höjd av 30-35 m. och kan få en stamdiameter av ända upp till 1 m. Till en
början högg man ned träden för att komma åt att tappa saften men denna
rovdrift hotade att utrota trädbeståndet. Numera vårdas gummiträden väl och
man gör skåror i barken utan att härigenom skada trädet, så att detta kan
tappas år efter år.
|
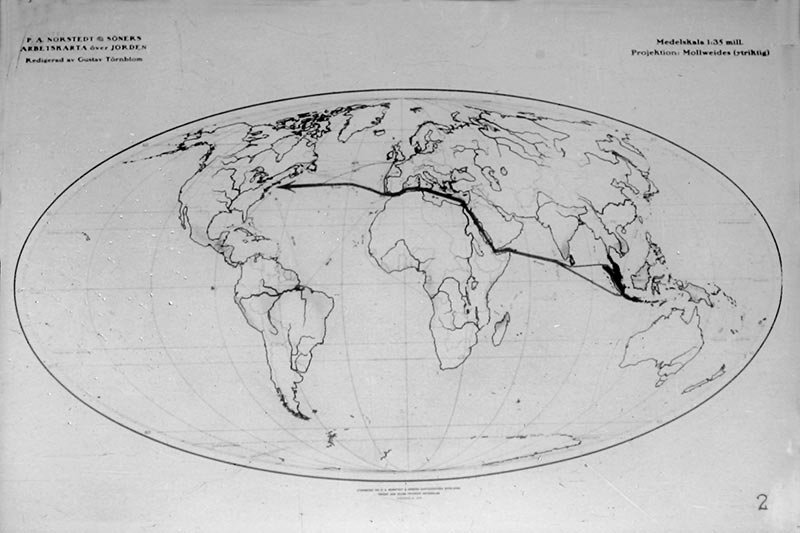 |
2. Kautschukförande växter finnas i ett bälte omkring ekvatorn runt hela
jorden. Genom plantor och frön lyckades man inplantera Heveaträdet i Afrika
och Asien. Större delen av gummiproduktionen kommer numera från plantagerna
på Malajstaterna, Holländska Indien och Ceylon och övervägande delen av
rågummit går till Amerika. Amazondistriktet, som från början ensamt försåg
världen med rågummi, har nu mindre betydelse. Ryssland har även en betydande
produktion av rågummi, som erhålles ur rötterna på vissa kautschukförande
växter. Likaså kan man i allt större utsträckning räkna med syntetiskt
gummi.
|
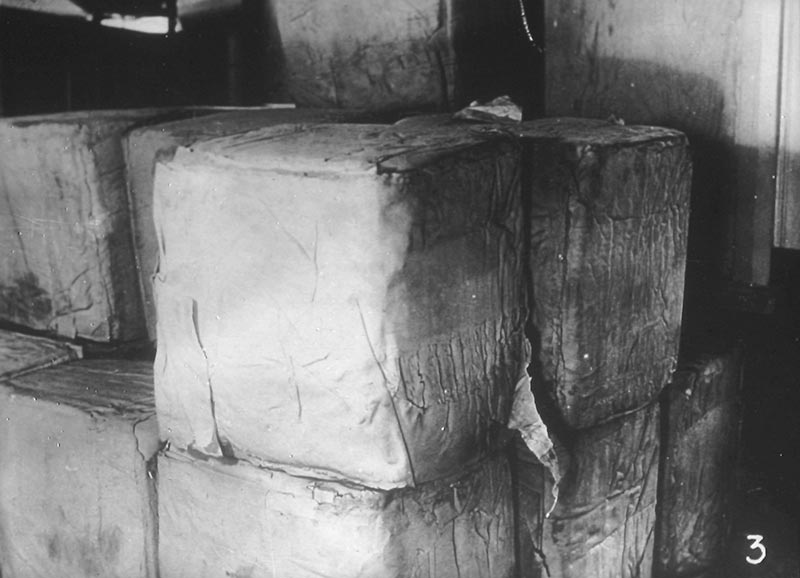 |
3. Den mjölkliknande vätska, som erhålles från de gummiförande träden
innehåller vanligen omkring 35 % kautschuk. Återstoden utgöres till större
delen av vatten. Genom tillsats av ättiksyra bringas vätskan att koagulera
så att kautschuken erhåller fast form. Den innehåller en del föroreningar
varför den måste tvättas och genomgå diverse behandlingar. Slutligen pressas
den mellan valsar ut till tunna ark, som buntas till balar. Sådant är
råvarans utseende, då den kommer till gummifabriken. Den tillsättes där
olika kemikalier och färgas, beroende på för vilket ändamål den skall
användas.
|
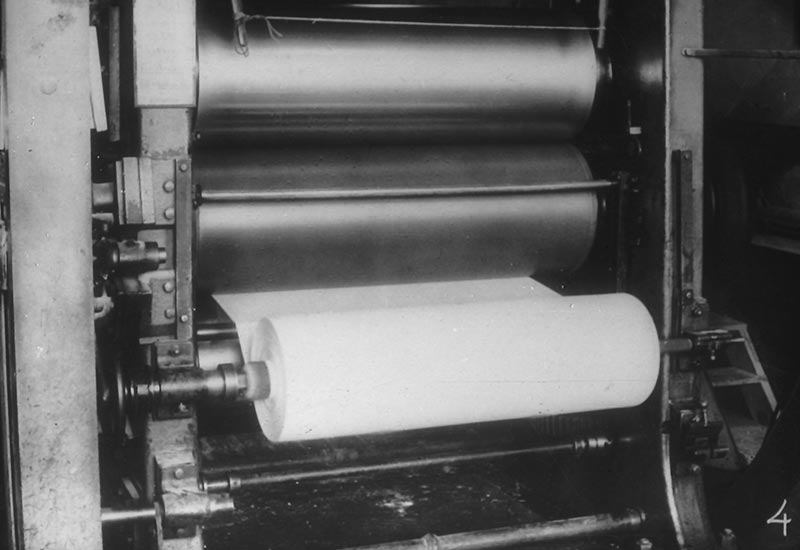 |
4. Rågummit uppmjukas först i ett valsverk. Här iblandas även de kemikalier,
som behövs för de olika blandningarna. Gummiblandningen kan nu gå till
kalandern, en maskin, som vanligen finns på alla gummifabriker.
Kalandern har oftast två uppgifter att fylla. Dels valsar den ut
gummiblandningen och dels pressas med densamma gummit in i vävnader.
Den vanligaste typen är 3-valskalandern, vars valsar äro anordnade för
värmning och kylning. Gummiblandningen uppvärmes och göres smidig i ett
mindre valsverk och matas in mellan de båda översta valsarna i kalandern,
går runt den mellersta valsen och ut mellan de båda nedersta. Bilden visar
hur den väv, som skall beläggas med gummi, matas in mellan de nedersta
valsarna.
|
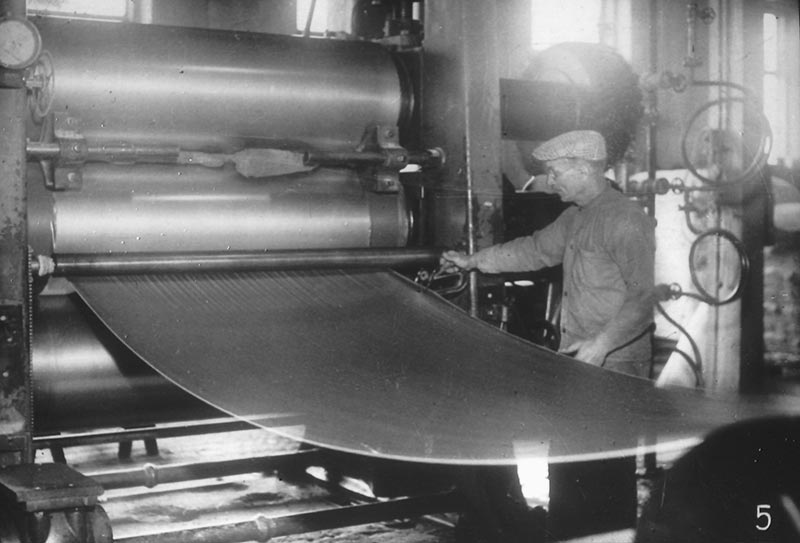 |
5. Då väven kommer ut från kalandern har ett tunt lager gummi pressats in i
densamma. Gummidukens tjocklek kontrolleras.
|
 |
6. Den kanske allra viktigaste användningen av gummi är för bil- och
cykeldäck. Utan dessa skulle den snabba trafiken på våra gator och vägar ej
vara möjlig. Ett bildäck består förutom av gummi av en del vävinlägg, som
öka hållfastheten och dessutom äro värmeisolerande. Denna väv kallas cordväv
och består av gummerad väv med parallellt liggande trådar, vilka ej ha någon
väft utan sammanhållas av gummit.
|
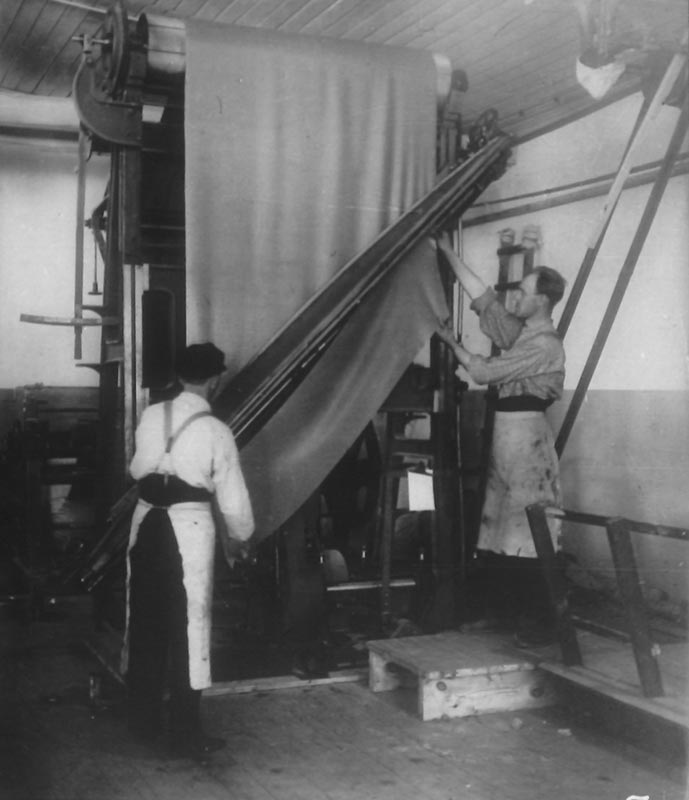 |
7. Cordväven skäres i ungefär 45 % vinkel samt i den bredd, som
däckdimensionen kräver.
|
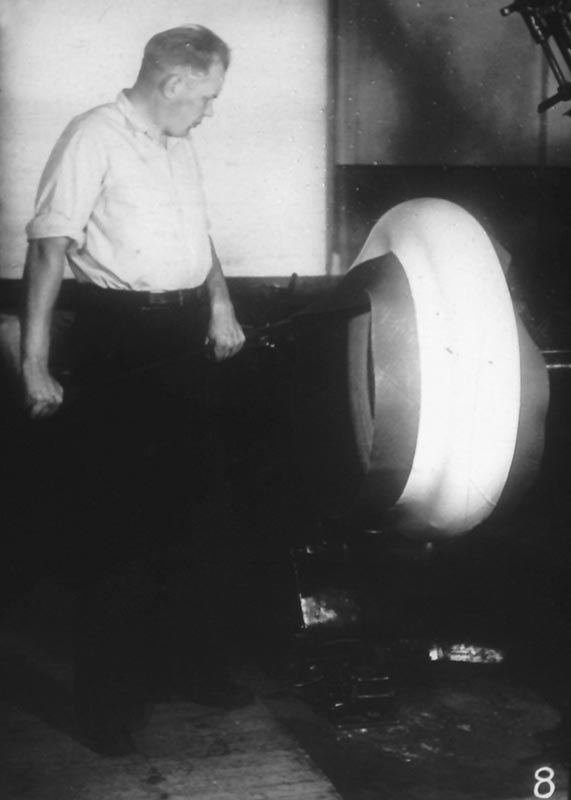 |
8. Cordväven lägges på en roterande ringstomme, en s.k. kärn. De olika
lagren läggas så, att trådarna i ett lager bilda ungefär 90°
vinkel med trådarna i nästa lager. Mellan vissa lager lägges en tunn platta
av mjukt gummi.
|
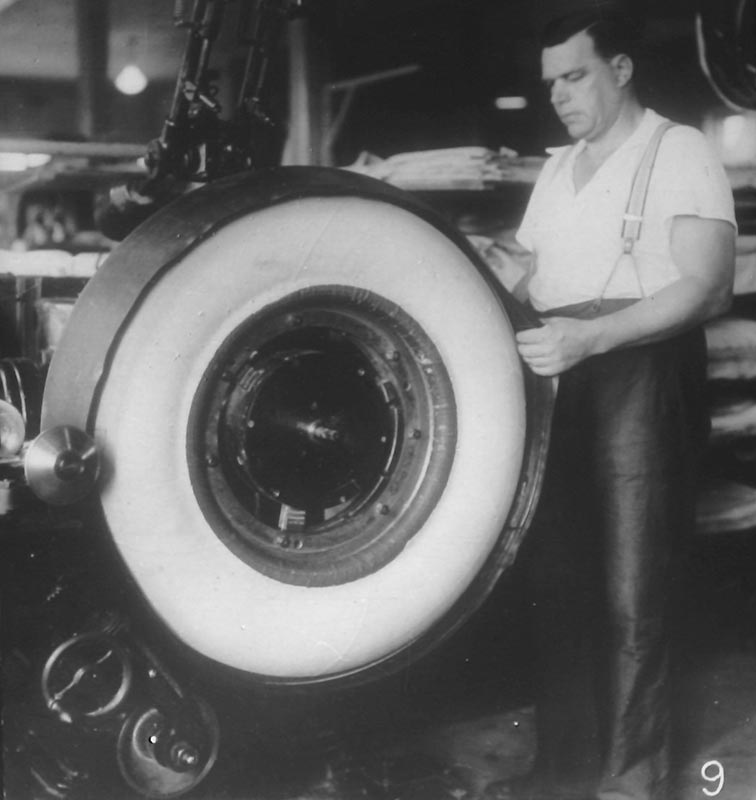 |
9. Då tillräckligt antal lager cordväv uppnåtts pålägges slitbanan av gummi.
Denna består av ett flertal lager av gummiplattor.
|
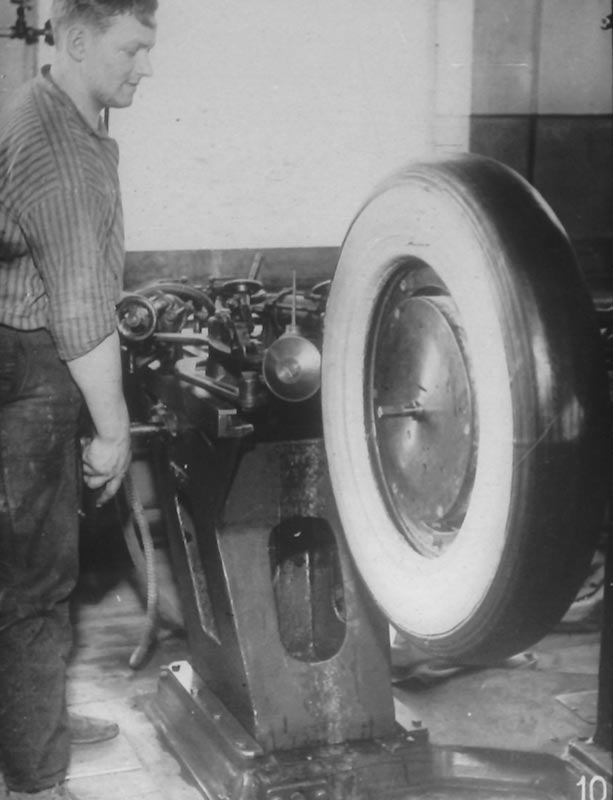 |
10. Ringen får nu rotera mot valsar, som pressa till gummit.
|
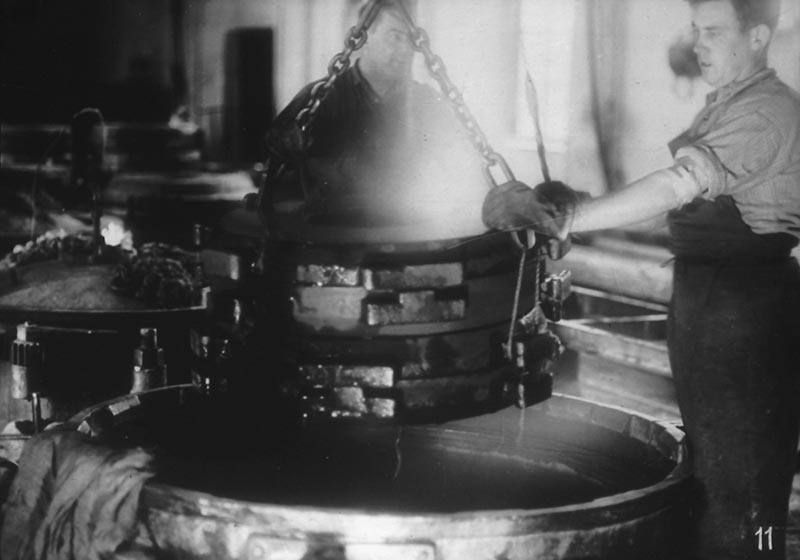 |
11. Då ringen är färdigbyggd, lägges den i en form och sänkes ned i
vulkaniseringspannan. Den stomme på vilken ringen byggts upp är nu borttagen
och man har lagt in en luftslang, som hålles uppblåst och pressar däcket mot
formens sidor. Ånga insläppes i vulkaniseringspannan och trycket får stiga
tills en temperatur av ungefär 135° uppnåtts.
Vulkaniseringen av de största bildäcken ta en tid av 2 ½ timmar.
|
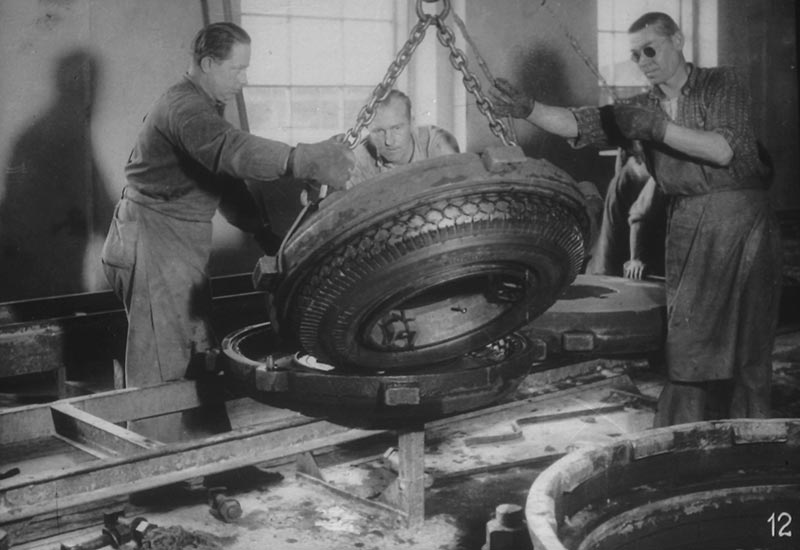 |
12. Formen tages ut ur vulkaniseringspannan och öppnas. Däcket är nu
färdigt. På insidan ser man tilledningen till den luftslang, som omnämnes på
föregående bild.
|
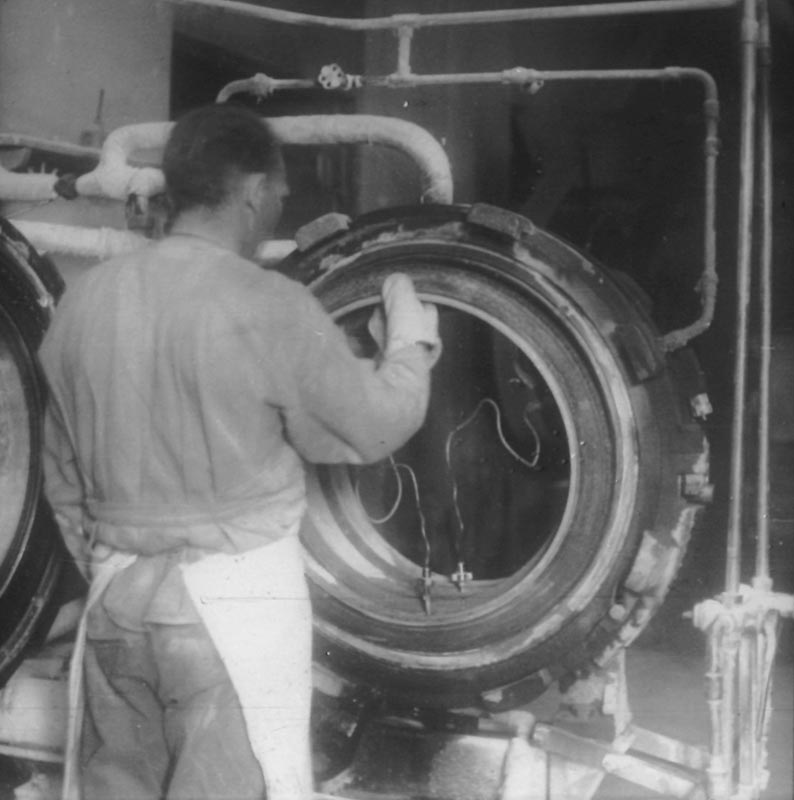 |
13. Ett cykeldäck kommer till på ungefär samma sätt. Påfrestningen på ett
sådant är ej så stor, varför dimensionerna kunna göras mindre. Bilden visar
två cykeldäck, inlagda i en stående vulkaniseringsform. Dels se vi ledningar
för tryckluft, en till varje däck, samt vidare de rör genom vilka ånga under
högt tryck tillföres. Vulkaniseringstiden är endast ca 8 min. och
temperaturen ca 165°.
|
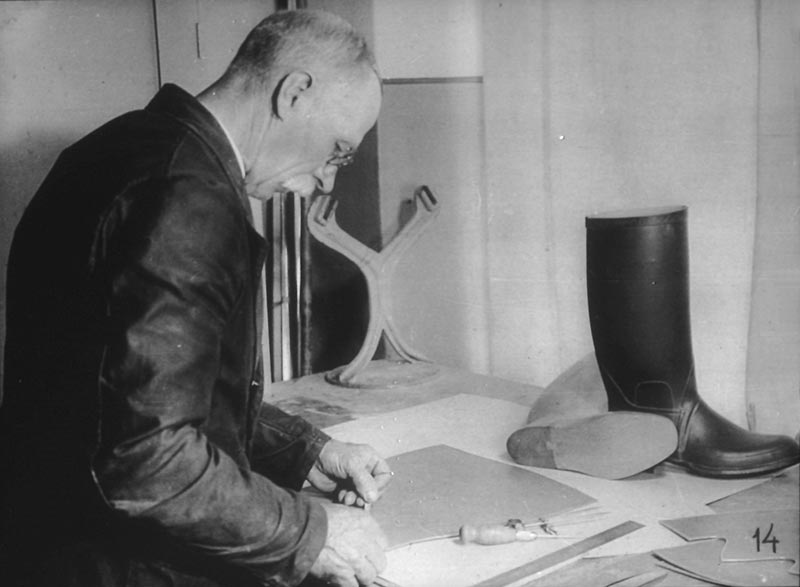 |
14. Då en gummistövel, galosch eller gummisko skall tillverkas, får man
först tillverka schabloner efter vilka de olika delarna skäras ut. Efter
dessa schabloner tillverkas stansverktyg.
|
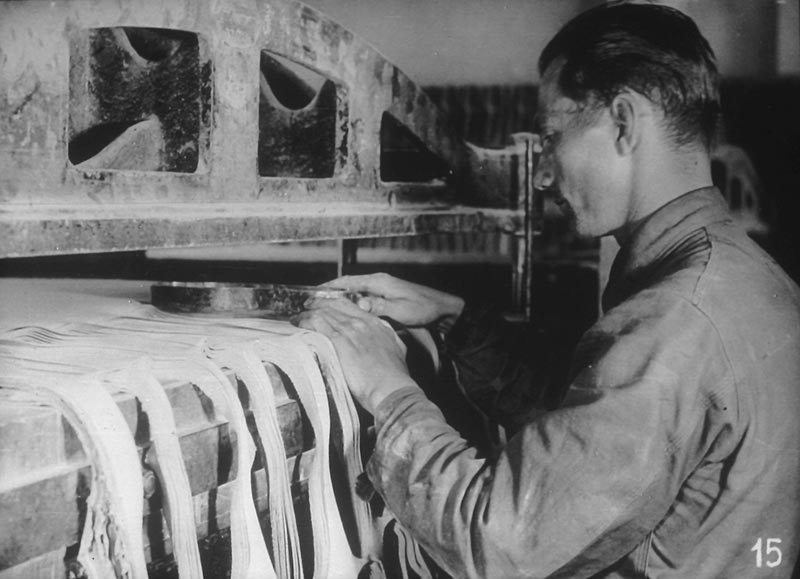 |
15. De olika delarna stansas ut i maskiner.
|
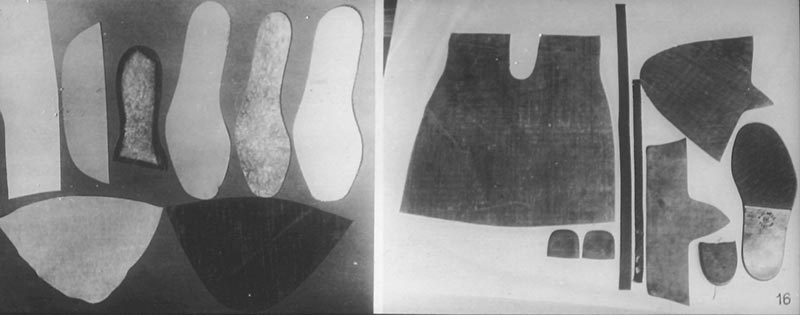 |
16. Alla dessa delar ingå i en gummistövel.
|
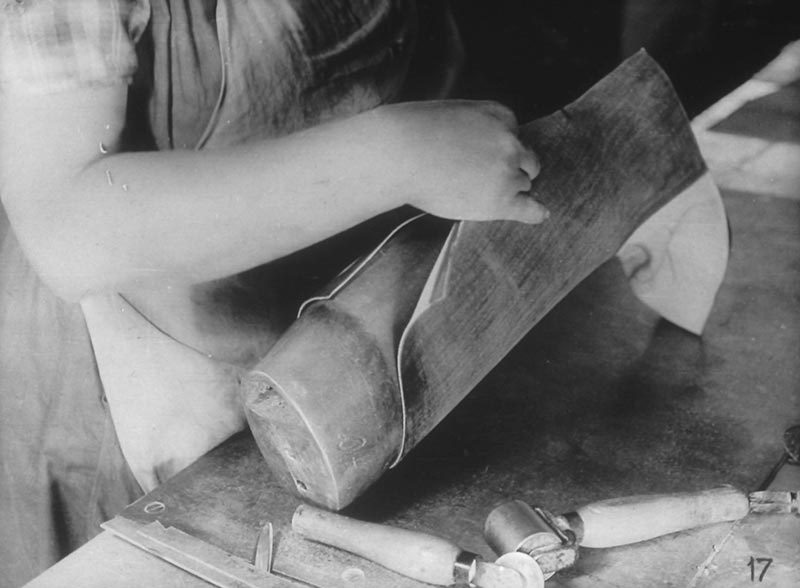 |
17. En gummistövel bygges upp på en läst av aluminium. Här lägges skaftet på
lästen.
|
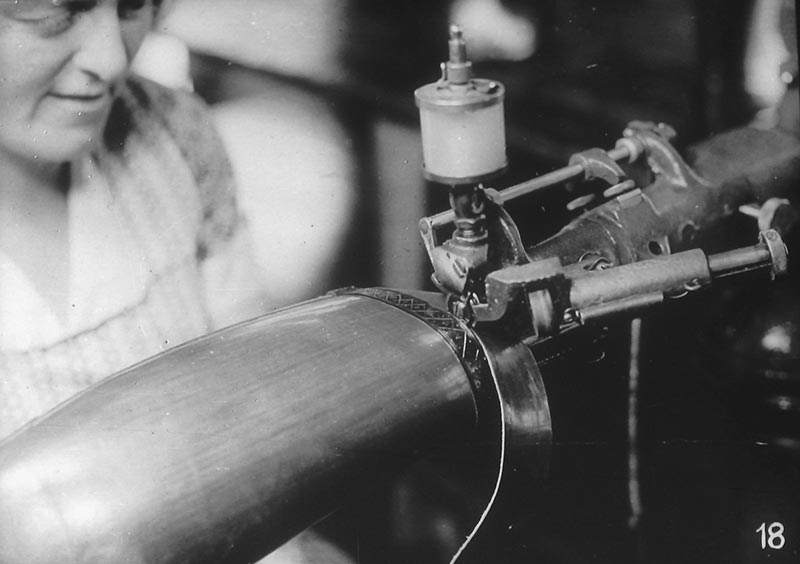 |
18. Upptill klippes skaftet jämt. Detta sker vanligen först efter
vulkaniseringen.
|
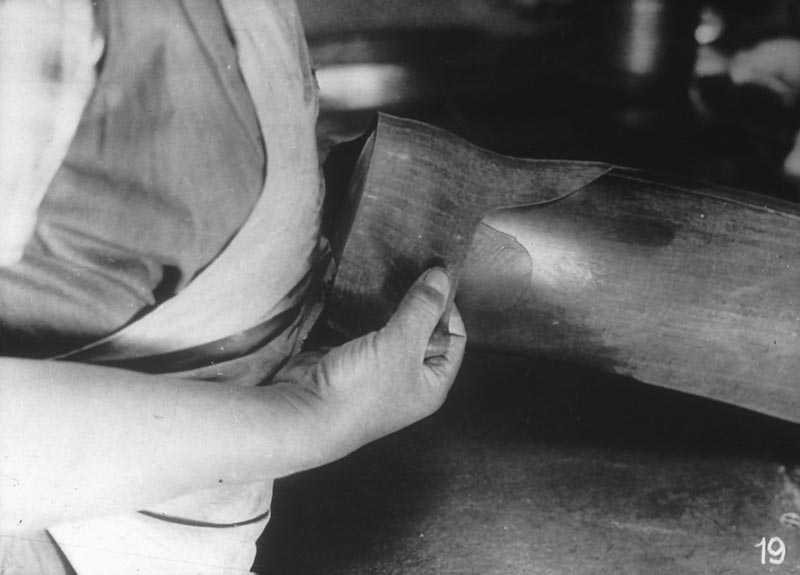 |
19. Skaftets nedre bakre del är utsatt för stor påfrestning och får därför
en förstärkning.
|
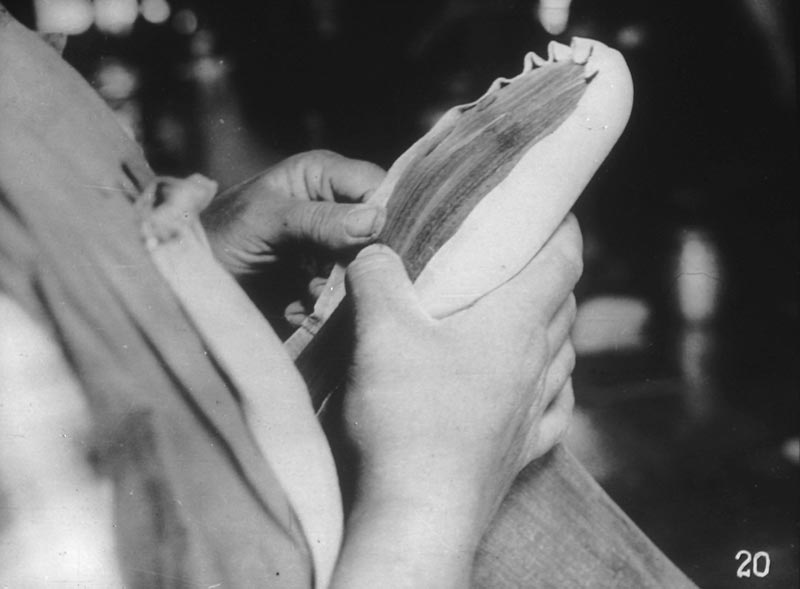 |
20. Stövelfodret pinnas på fodersulan.
|
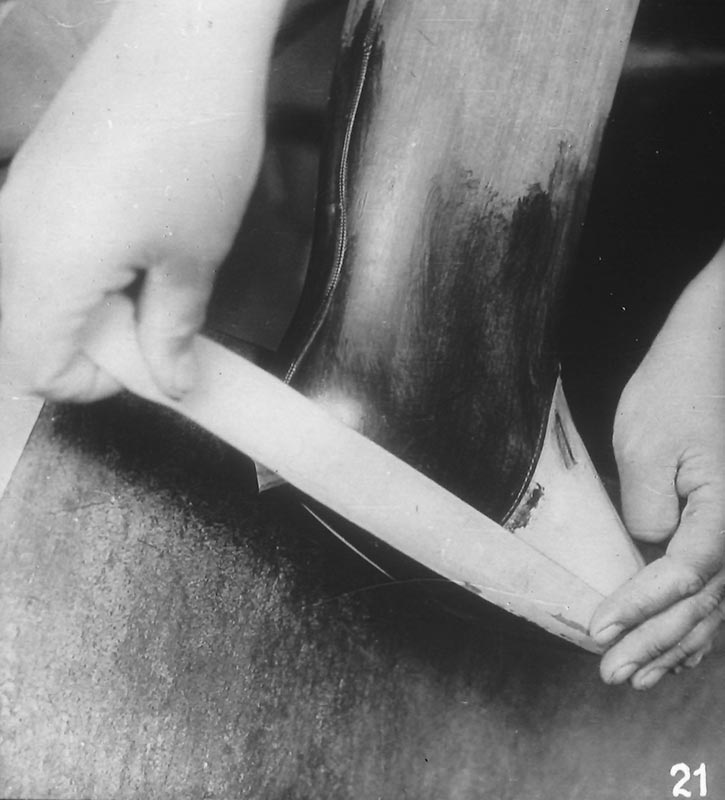 |
21. Sedan lägges en extra förstärkning runt stövelfoten och slutligen sulan.
Därefter är stöveln färdig att gå till vulkaniseringsavdelningen.
|
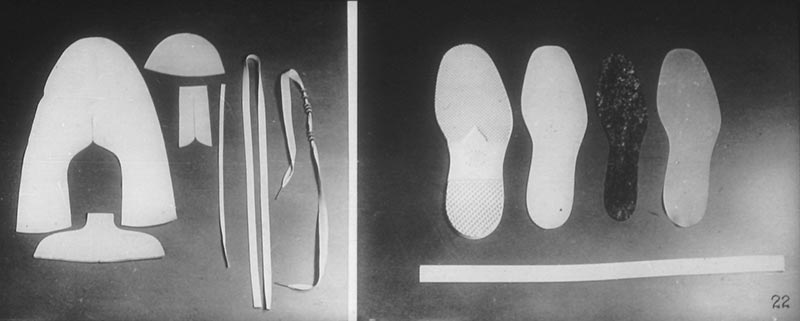 |
22. Dessa delar ingå i en gymnastiksko.
|
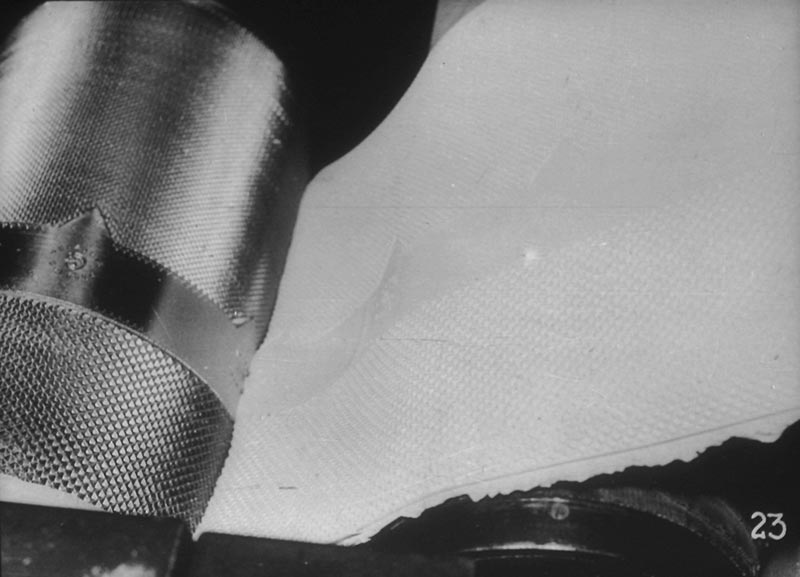 |
23. Sulgummit valsas ut, varefter sulan sedan skäres på en sulskäringsmaskin.
|
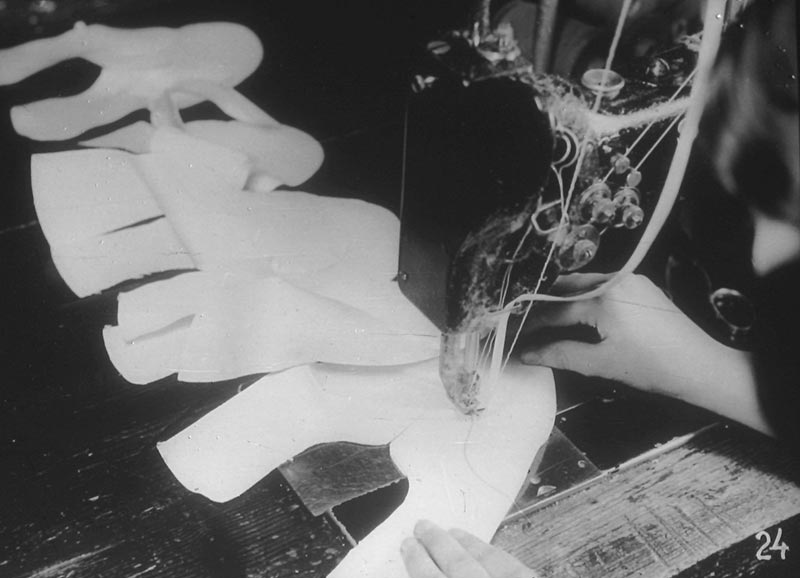 |
24. Överdelen av tyg sys ihop och förses med garneringsband.
|
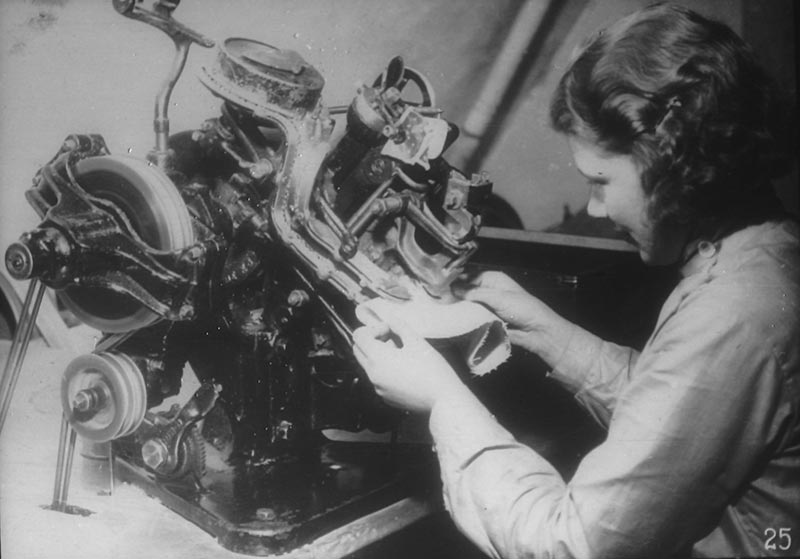 |
25. I en maskin sättes märlorna i snörhålen.
|
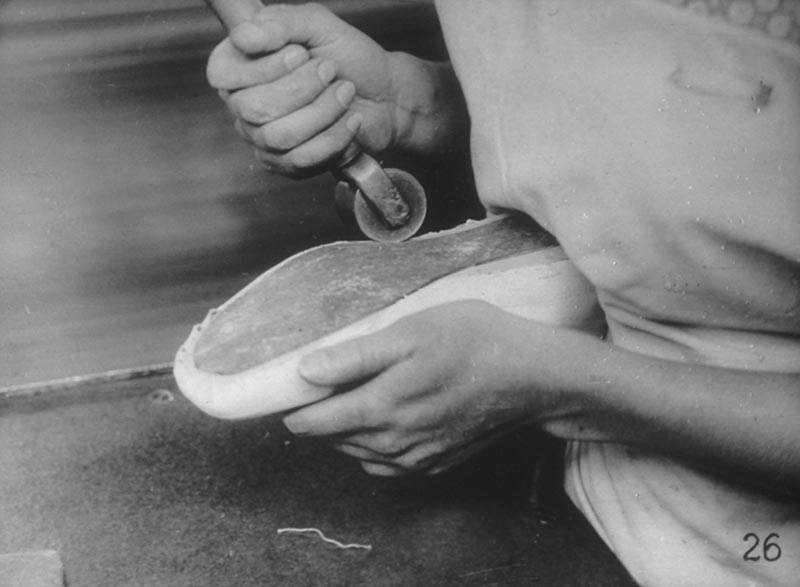 |
26. Då överdelen, nåtlingen, är hopsydd lägges den över en läst och uppinnas
mot fodersulan.
|
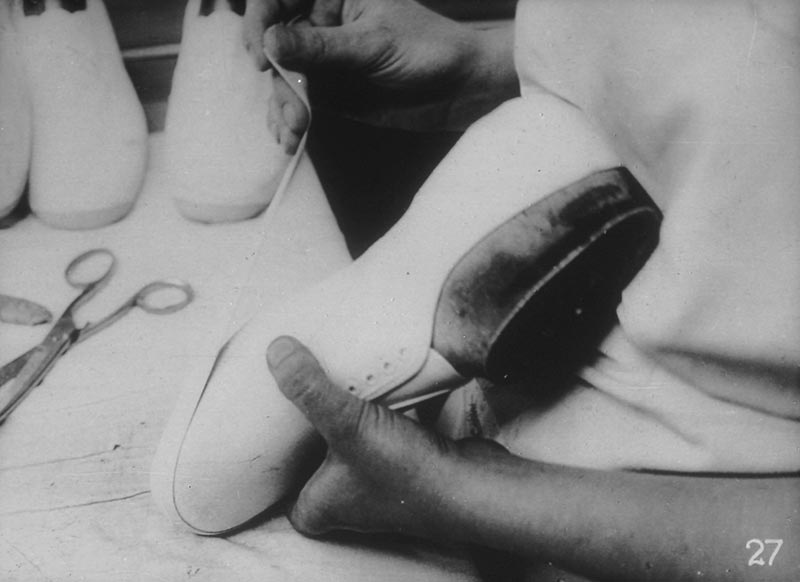 |
27. Därefter lägges kantbandet av gummi på ...
|
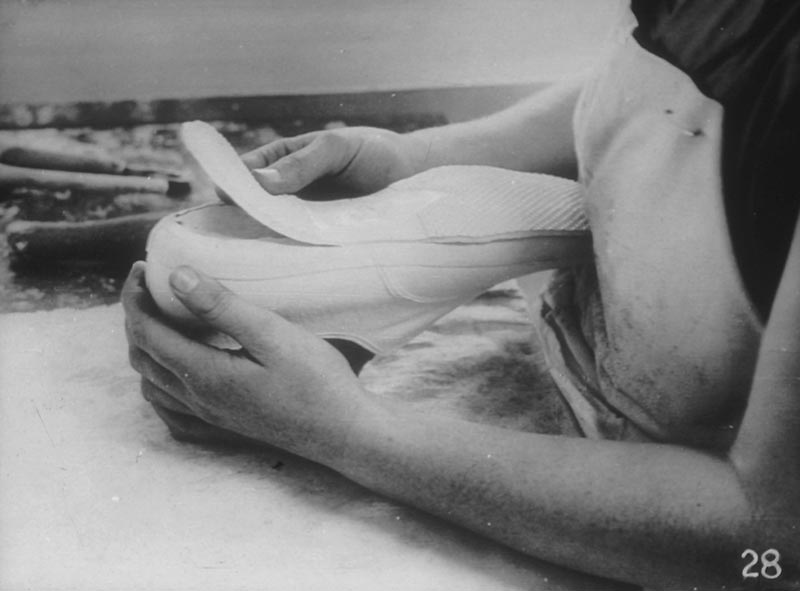 |
28. ... och slutligen sulan.
|
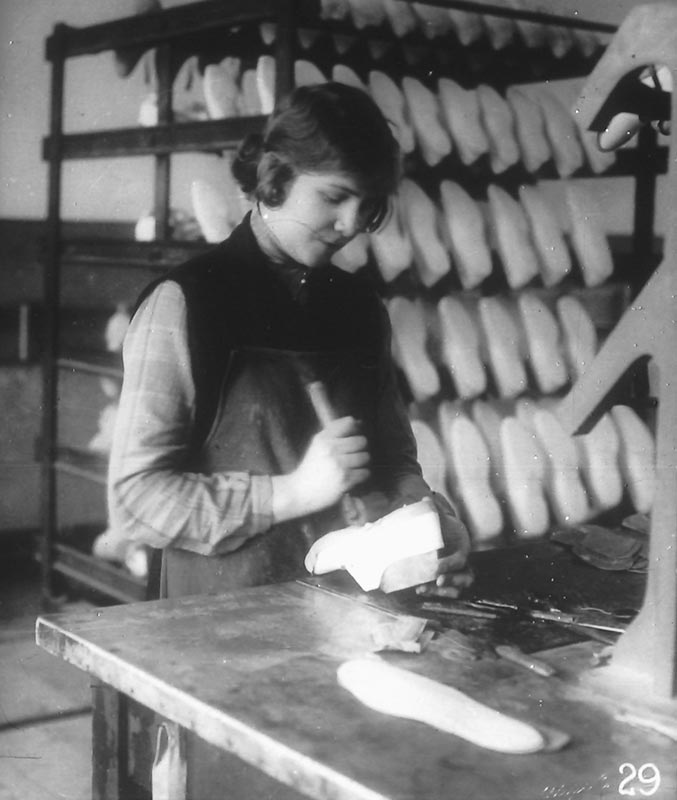 |
29. Här bygges en lätt skommarsko upp på en aluminiumläst. Då den är
upplästad, sättes den på vagnen, vilken köres direkt in i
vulkaniseringsugnen.
|
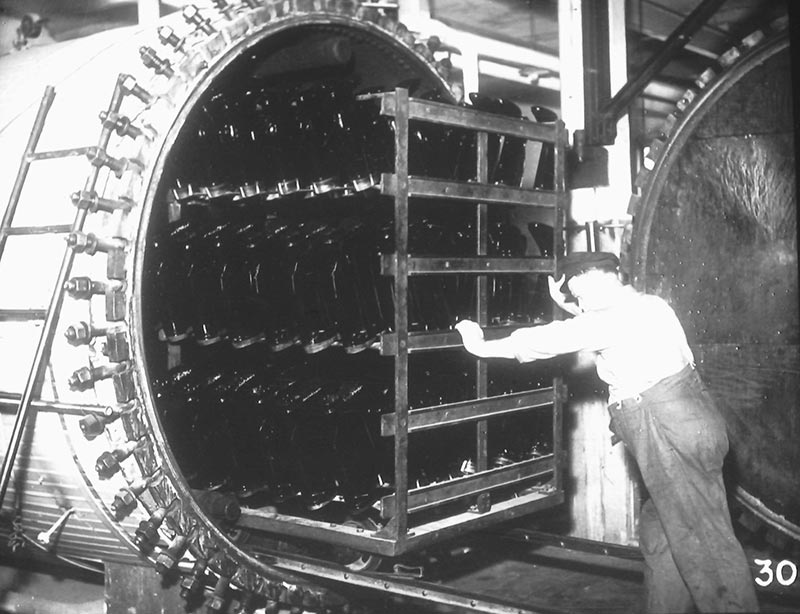 |
30. Vulkaniseringspannorna äro vanligen stora runda cylindrar, där vagnar
med gummivaror köras direkt in. Temperaturen i en sådan ugn varierar,
beroende på vilka artiklar som skola vulkaniseras.
|
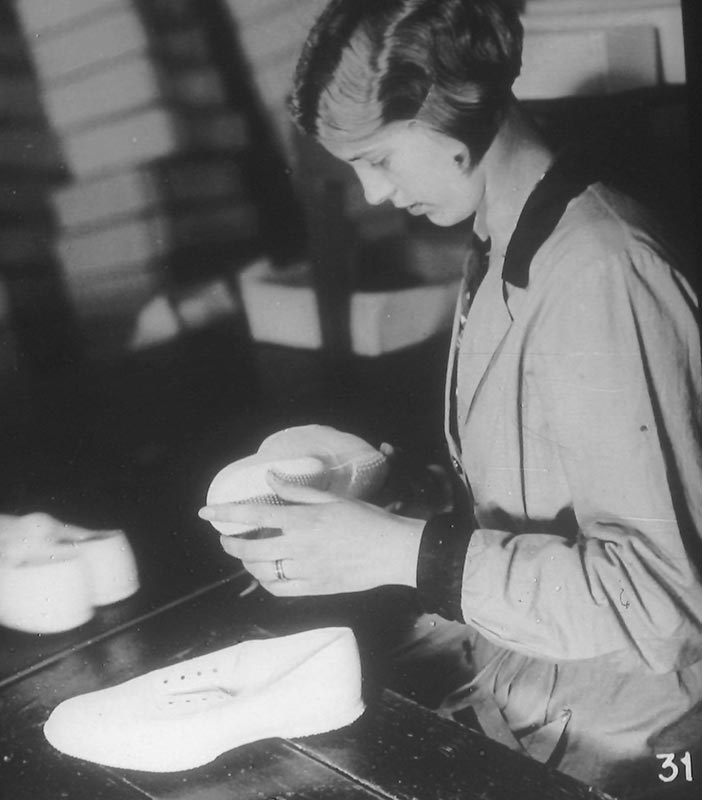 |
31. Den färdiga gymnastikskon har efter vulkaniseringen tagits av lästen och
avsynas.
|
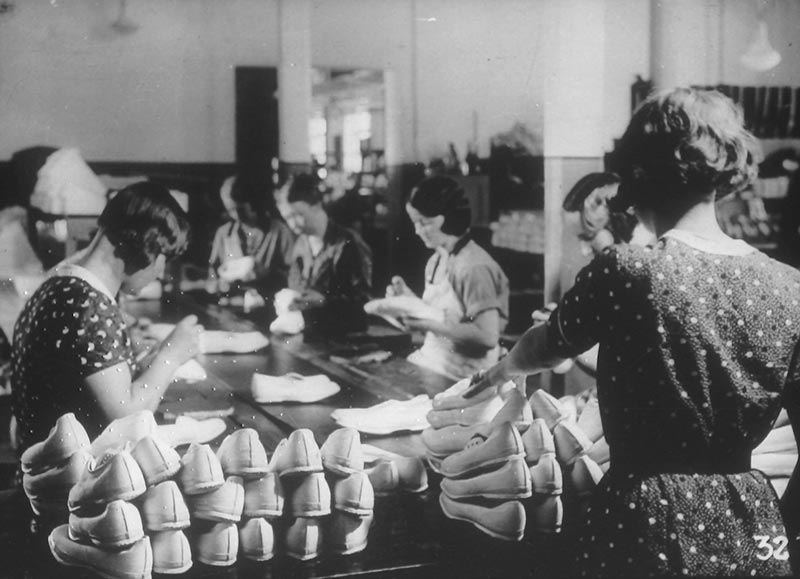 |
32. Gymnastikskorna komma här på löpande band. De märkas och packas in i
kartonger.
|
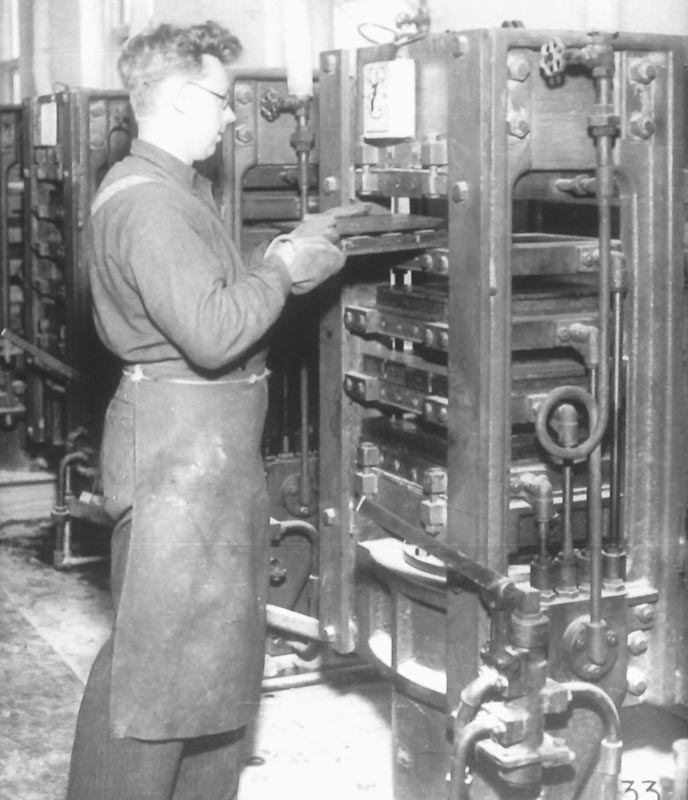 |
33. Här vulkaniseras gummiklackar och sulor i en hydraulisk press.
|
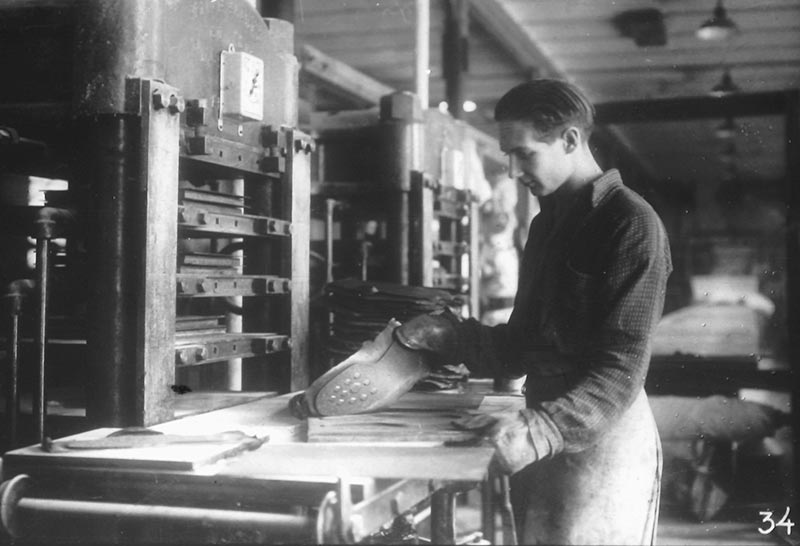 |
34. En färdig gummisula tages ut ur pressen.
|
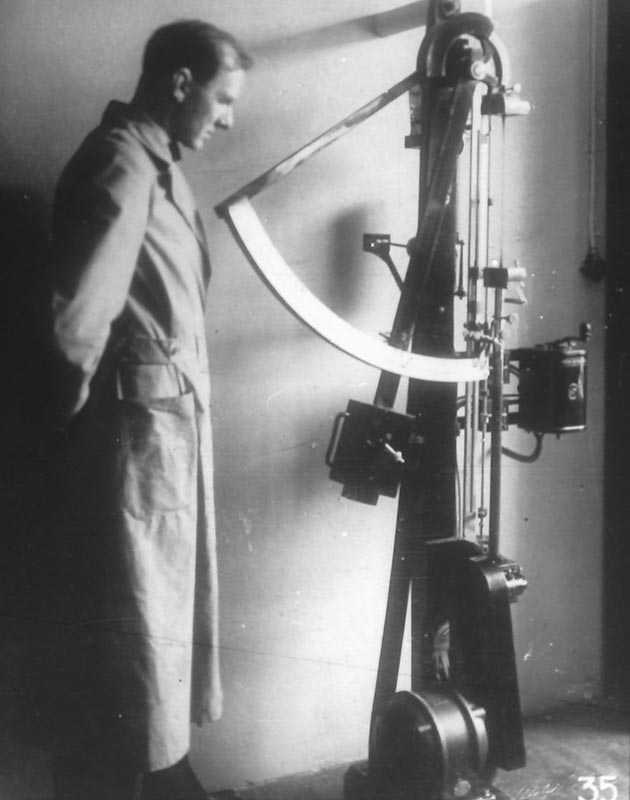 |
35. Från rågummit till den färdiga varan tages i fabriken upprepade prov.
Särskilt har utförandet av vulkaniseringen stor betydelse för hållbarheten.
På maskinen synes längst till höger en smal gummiremsa, vars hållfasthet
provas.
|
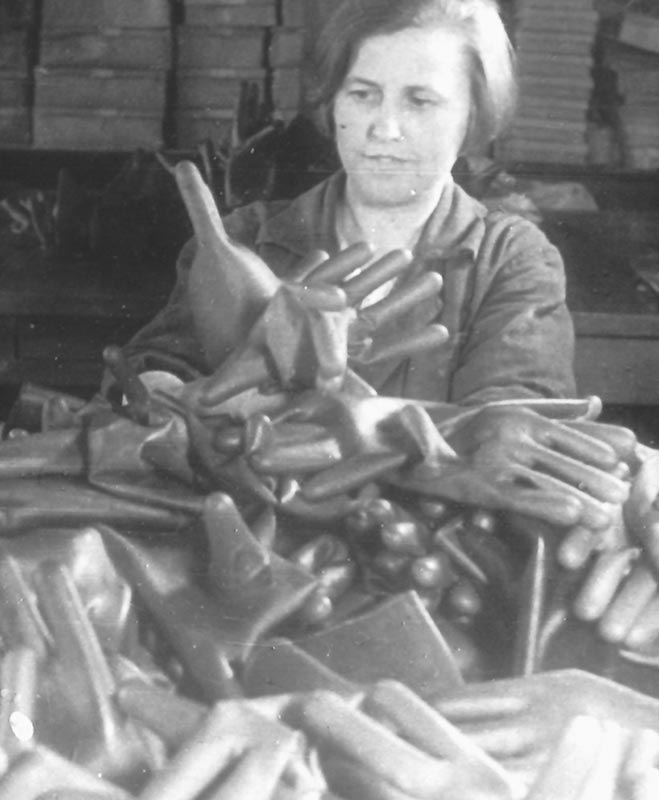 |
36. Gummihandskar användas i stor utsträckning inom sjukvård, industri,
skogs- och bergsbruk o.s.v. De tillverkas på så sätt, att en porslinsmodell
av en hand upprepade gånger doppas ner i en latexblandning eller en
bensinlösning av gummi. Då gummit fått önskad tjocklek, vulkaniseras det,
varefter handsken drages av och är färdig.
|
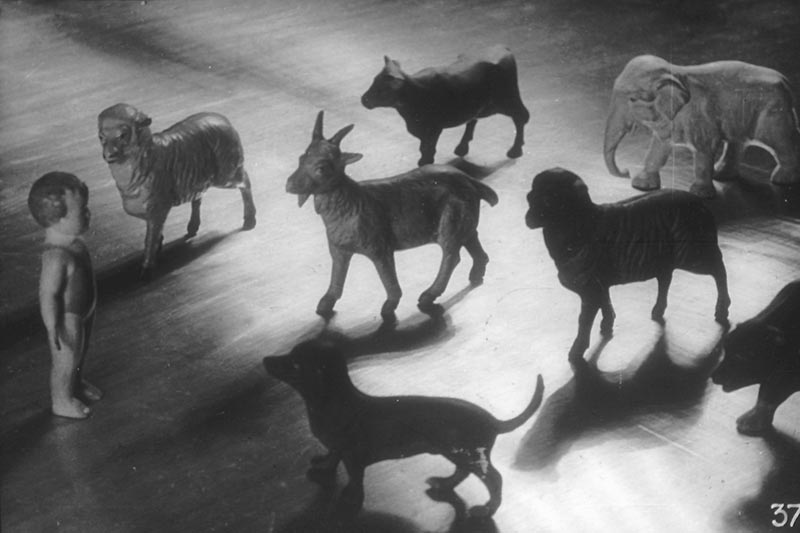 |
37. Gummi är hygieniskt, lätt att hålla rent samt hållbart varför det har
fått stor användning på de mest skilda områden. Som sista bild i denna serie
visa vi några leksaker av gummi - lätta att hålla rena samt hållbara -
vilket har sitt värde då de ena stunden stoppas i munnen för att kanske
ögonblicket därefter kastas på golvet eller tvärtom.
|
Bildmaterialet till denna serie har ställts till förfogande av Svenska
Gummifabriks Aktiebolaget, Gislaved.
P. A. Norstedt & Söner.
|
|
|